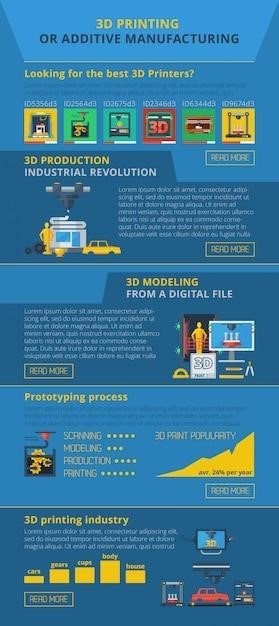
Production Layout Guide⁚ A Comprehensive Overview
This guide provides a comprehensive overview of production layout‚ a crucial aspect of factory management. It outlines the benefits‚ types‚ and steps involved in designing a production layout that optimizes efficiency and effectiveness. We’ll explore different layout configurations‚ delve into the importance of planning‚ and provide insights into the implementation process. This guide aims to equip you with the knowledge and tools necessary to create a production layout that aligns with your specific needs and objectives.
Introduction
A production layout‚ also known as a plant layout‚ is the physical arrangement of machinery‚ equipment‚ workstations‚ and storage areas within a manufacturing facility. It’s a fundamental aspect of production planning that directly impacts efficiency‚ productivity‚ and overall operational success. A well-designed layout optimizes material flow‚ minimizes waste‚ and enhances worker safety‚ ultimately contributing to a more streamlined and cost-effective manufacturing process. This guide will explore the importance of production layout‚ its various types‚ and the steps involved in designing a successful layout for your specific needs.
Benefits of a Production Layout
A well-planned production layout offers numerous benefits that can significantly enhance the efficiency and profitability of a manufacturing operation. By optimizing the flow of materials‚ minimizing unnecessary movement‚ and creating a more ergonomic work environment‚ a good layout can lead to⁚
- Increased productivity⁚ A streamlined layout reduces wasted time and effort‚ allowing workers to focus on their tasks more efficiently.
- Reduced costs⁚ By minimizing material handling and transportation‚ a well-designed layout can lead to lower operating costs and increased profitability.
- Improved product quality⁚ A more organized and efficient workflow can lead to fewer errors and higher product quality.
- Enhanced safety⁚ A clear and safe layout promotes worker safety by reducing potential hazards and accidents.
- Increased flexibility⁚ A well-designed layout can be adaptable to changes in production needs‚ allowing for future growth and expansion.
These benefits highlight the importance of carefully planning and implementing a production layout that aligns with the specific requirements of your manufacturing operation.
Types of Production Layouts
Production layouts can be categorized into several types‚ each with its unique characteristics and suitability for different manufacturing processes. The four primary types of production layouts are⁚
- Process layout⁚ This layout groups similar machines or operations together. It is ideal for manufacturing operations with high product variety or low production volumes.
- Product layout⁚ This layout arranges machines and equipment in a linear sequence‚ resembling an assembly line. It is suitable for high-volume‚ standardized production of a single product or a few similar products.
- Fixed-position layout⁚ In this layout‚ the product remains in a fixed location while workers‚ equipment‚ and materials move around it. This layout is used for large‚ complex products that cannot be easily moved‚ such as ships or airplanes.
- Cellular layout⁚ This layout combines elements of process and product layouts‚ creating smaller‚ self-contained production cells dedicated to producing a specific product or family of products.
Choosing the most appropriate layout type for your manufacturing operation is a crucial step in optimizing production efficiency and effectiveness.
Process Layout
A process layout‚ also known as a functional layout‚ groups similar equipment or operations together‚ regardless of the specific product being manufactured. This layout is characterized by a high degree of flexibility‚ allowing for the production of a wide variety of products. It is particularly suitable for industries that produce customized goods‚ handle small batch sizes‚ or deal with high product variability. Examples of industries that utilize process layouts include machine shops‚ hospitals‚ and repair shops. The main advantage of a process layout is its adaptability to different product types and production requirements. However‚ it can also lead to longer material handling times‚ increased work-in-process inventory‚ and potential inefficiencies if the flow of materials is not well-managed.
Product Layout
A product layout‚ often referred to as a line layout‚ is a highly structured arrangement where workstations and equipment are positioned in a sequential order‚ mirroring the steps involved in producing a specific product. This layout is ideal for mass production environments where high volumes of identical or very similar products are manufactured. A classic example is an assembly line for automobiles. The product layout emphasizes efficiency‚ minimizing material handling and maximizing production throughput. It typically involves specialized equipment and tasks‚ leading to high levels of productivity and lower per-unit costs. However‚ this layout lacks flexibility‚ making it less suitable for diverse product lines or frequent product changes.
Fixed-Position Layout
The fixed-position layout‚ also known as a project layout‚ is a distinct approach where the product remains stationary while resources‚ equipment‚ and workers move around it. This layout is employed when dealing with large‚ complex‚ or immobile products‚ such as ships‚ aircraft‚ or large construction projects. The advantage lies in its ability to accommodate intricate and customized work‚ allowing for focused attention and specialized equipment. However‚ coordination and material handling become critical as workers and resources must navigate around the fixed product‚ potentially leading to logistical complexities and increased costs. This layout excels in situations where mobility is limited‚ requiring a tailored approach to production.
Cellular Layout
The cellular layout‚ also known as group technology‚ is a flexible approach that focuses on grouping similar products or components into production cells. Each cell is self-contained‚ housing the equipment and workers necessary to manufacture a specific family of products. This layout promotes efficiency and reduces work-in-progress inventory by streamlining the flow of materials within each cell. It fosters cross-training among workers‚ increasing their versatility and adaptability. The cellular layout is particularly effective for companies producing a variety of products with similar processes or components. It promotes a lean manufacturing philosophy by minimizing waste and maximizing efficiency through focused production.
Steps for Designing a Production Layout
Designing a production layout requires a systematic approach to ensure it aligns with your company’s goals and operational needs. The process involves several steps‚ each contributing to the development of an effective and efficient layout. This structured approach helps minimize errors‚ optimize resource allocation‚ and create a layout that supports your production objectives. A well-designed layout enhances productivity‚ reduces waste‚ and facilitates smooth workflow‚ ultimately contributing to the success of your manufacturing operations.
Step 1⁚ Collect Background Information
Before embarking on the layout design process‚ it’s crucial to gather comprehensive background information about your production process. This step involves understanding your company’s current operations‚ including the products manufactured‚ production volumes‚ and material flow. Delving into existing layout configurations‚ if any‚ is essential to identify areas for improvement. Collecting data on equipment‚ machinery‚ and their specifications is crucial for determining space requirements and layout constraints. Furthermore‚ gathering information on workforce size‚ skillsets‚ and safety regulations ensures a layout that accommodates personnel needs and safety standards. This thorough data collection sets the foundation for an effective layout design.
Step 2⁚ Define Objectives and Constraints
Once you have gathered the necessary background information‚ the next step is to clearly define your objectives and constraints for the production layout. These objectives might include maximizing productivity‚ minimizing material handling costs‚ reducing production lead times‚ or enhancing product quality. Constraints can include available space‚ budget limitations‚ existing infrastructure‚ and safety regulations. A thorough understanding of these objectives and constraints will guide your layout design decisions. For example‚ if minimizing material handling costs is a key objective‚ you might consider a layout that reduces the distance materials need to travel. Similarly‚ if available space is limited‚ you might need to explore more compact layout options.
Step 3⁚ Develop a Rough Layout
With your objectives and constraints clearly defined‚ you can start developing a rough layout. This initial layout should be a schematic representation of the proposed production facility‚ showing the placement of key equipment‚ workstations‚ and material flow paths. You can use simple tools like graph paper or specialized software for this step. The rough layout should be iterative‚ meaning you can adjust and refine it based on feedback and analysis. This step involves considering factors like the sequence of operations‚ material handling requirements‚ and ergonomic considerations. For example‚ you might want to place heavy equipment close to loading docks to minimize material handling distances.
Step 4⁚ Refine the Layout
Once you have a rough layout‚ it’s time to refine it based on detailed analysis and feedback. This step involves evaluating the rough layout against key performance indicators (KPIs) such as production capacity‚ material handling efficiency‚ and worker safety. You can use simulation software to create virtual models of the proposed layout and test different scenarios. This allows you to identify potential bottlenecks and optimize the flow of materials and people. The refinement process may involve adjusting the placement of equipment‚ workstations‚ and storage areas to improve efficiency‚ reduce waste‚ and enhance overall productivity. This iterative process ensures that the final layout meets your objectives and addresses any constraints.
Step 5⁚ Implement and Evaluate
Implementing the refined layout involves physically rearranging equipment‚ workstations‚ and storage areas according to the finalized plan. This step requires careful coordination to minimize disruptions to ongoing production. Once implemented‚ the layout should be rigorously evaluated to assess its effectiveness. This involves tracking key performance indicators such as production output‚ material handling costs‚ and worker productivity. The evaluation process may reveal areas for further improvement‚ such as adjustments to equipment placement‚ workflow optimization‚ or training programs for workers. This ongoing evaluation ensures that the layout remains efficient and effective in the long term‚ adapting to changing production needs and market demands.
A well-designed production layout is a cornerstone of efficient and effective manufacturing operations. By considering the principles outlined in this guide‚ businesses can optimize their factory space‚ streamline workflows‚ and maximize productivity. The process involves a meticulous balance of planning‚ analysis‚ and implementation‚ ensuring a layout that meets the specific needs of the production process. Regular evaluation and adjustments are essential for maintaining efficiency and adaptability in a dynamic manufacturing environment. By embracing the principles of production layout design‚ businesses can achieve significant improvements in operational performance‚ ultimately leading to increased profitability and competitive advantage.